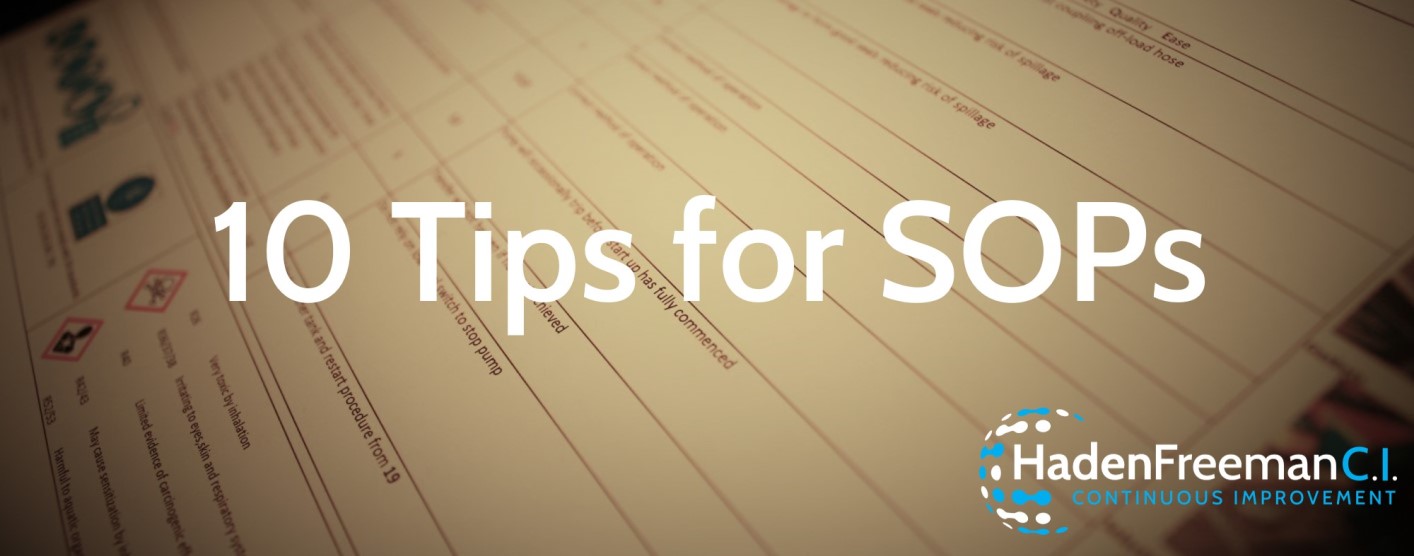
Consulting
January 26, 2021
10 Top Tips for SOPs
SOPs (Standard Operating Procedures) are critically important documents for any organisation – particularly so for regulated industries such as high hazard chemical plants (COMAH) and pharmaceutical manufacturers where deviations can cause major accidents or threats to patient safety.
SOPs are also known as Work Instructions, Job Instructions, Work Element Sheets, Job Element Sheet, amongst others. It is a bit confusing sometimes.
So today we are going to count down through some top ten tips to our number 1 tip.
10. Good SOPs are a solution to many problems.
- Get your SOPs right and many issues and human errors will reduce or disappear, such as variable job execution, non-compliances(violations), rule based mistakes, and errors of misunderstanding.
9. SOPs are not a solution to every problem.
- There is a great tendency and temptation to amend an SOP as a knee jerk reaction to any and every failure to follow the procedure. This is particularly common in pharma where deviations leading to CAPAs often default to “human error” with an action to “amend the SOP”. This just makes the SOP longer and longer, and fundamentally harder to read so increasing the probability of variation. And if the error was a slip or a lapse amending the SOP will not help anyway.
8. You cannot just copy automotive.
- Lean style SOPs which are being adopted throughout many industries originate in automotive. However, automotive is a different environment to chemicals, pharma, or indeed any other type of industry (and each automotive company has its own idiosyncrasies) meaning you cannot copy what an automotive company has done – you are not the same company. In particular there can be issues and confusion around the applicability of Standard Work documents and the differences between an engineering standard and an SOP.
7. You must adapt and apply the principles.
- While you cannot copy an automotive implementation of SOPs, the underlying principles are good and therefore when implementing Lean style SOPs it is important to copy and apply the principles. This may lead to quite a different and better implementation than simply copying an automotive approach would have done.
6. Pay attention to the detail.
- This is in two parts – layout and content.
- Getting the layout correct will help in both the drafting of SOPs and in accurately reading and following SOPs.
- The aim of a well written SOP is to capture all the known knowledge and best practice in undertaking a task to prevent loss of knowledge, so the detail of the content is also important.
5. Easy to update.
- Unless your SOPs are easy to update they will not be kept up to date. Therefore, the updating process should be simple and easy to use.
4. Must always be controlled document with change control.
- SOPs must be document controlled with good change management. SOPs are the foundation of your process control and product quality, so allowing uncontrolled changes is out of the question, even more so for hazardous and critical processes. However, making this process slick and easy is super critical otherwise they are no longer easy to update.
3. Leverage the whole workforce to keep them up to date.
- Updating procedures is time consuming. Often the ability to amend and update procedures, and to authorise changes, is reserved for more senior staff. This will cause bottlenecks in the updating process which serves as a barrier to updating SOPs. Look for ways to use the whole workforce to update procedures so spreading the load, making the task easier.
2. The SOP must reflect what occurs, not dictate what should happen.
- Beware of discrepancies between the SOP and what occurs. Pushing responsibility down the organisation for keeping SOPs up to date down will lead to SOPs that reflect what occurs, giving better adherence and exposing issues and problems that can then be addressed, driving continuous improvement.
1. SOPs MUST be user centric.
- This may seem obvious, but at some sites this has been a fundamental sea change in approach. SOPs do not exist for auditors or the HSE or the EA or anyone else other than the user. Having a user focus changes the SOP approach and content – dropping background information and explanations irrelevant to the user at the time of doing the job – making the SOP focused and honed, becoming easier to read and more useful to the user so the SOP is referred to more often. This all leads to improved adherence. Oddly enough, you may find that auditors, regulators and other stakeholders want this too.